Handling of man-made Objects using automated Positioning, Planning and Enhanced Reasoning methods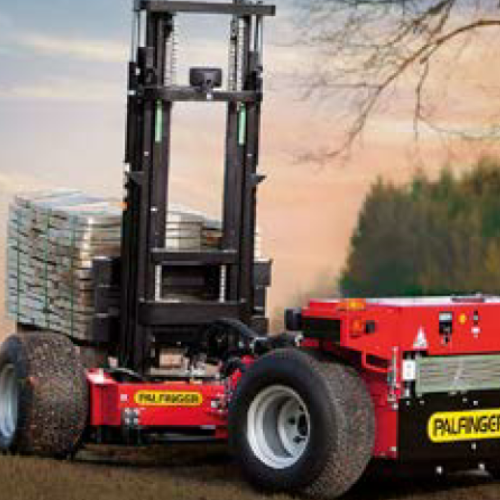
Production and transport processes of the future will mostly involve operations carried out by autonomous robots. This demand for automation is not solely driven by the will to enhance cost- and work-efficiencies, but also due to the ongoing changes in society where professions involving simple, monotonic work processes are quickly losing attractivity. The resulting shortage of workers thus represents a certain burden towards further economic and industrial development.
Converting human work processes into automated workflows is, however, not without challenges. Analogous to trained human workers, certain tasks require sophisticated hand-eye coordination and maintaining an awareness of the surroundings. Machine-assisted handling of goods is such a scenario where spatially accurate positioning and planning of movement are recurring operational steps.
In this project we seek to automate a broad set of operations: handling of man-made objects in different applied task settings like loading and unloading. To execute complex operations between multiple large-sized machines/objects, reaching centimetre-level accuracy requires an unambiguous abstraction of the surrounding scene and its relations. Our proposed technological answer to the task-specific challenges is based on a set of complementing representations and optimal motion planning incorporating nonlinear constraints.
In the process from sensing to reasoning and control we will address the following key research targets: understanding the scene and its relations, robust pose estimation and tracking employing multiple object-pose-specific cues, exploiting simulation and data synthesis to optimize sensor placement and cope with the data need of modern learning techniques.
HOPPER offers exciting perspectives due to multiple aspects: solving the envisioned automated operation task has a far-reaching impact, since the project’s specific use-cases can be mapped to a broad set of work processes involving complex interaction and object manipulation. Project partners are highly complementary as they span the whole range from technology concept, robot sensing and control to technology on-the-field validation.
In addition, in selected, so-far unsolved areas we anticipate creating new research results of great practical impact. The project outcome shall yield a re-configurable and extensible robotic functional module, capable to operate in outdoor environments at various scales (such as palette loading, automated crane).
Research Topics
Automated Systems, Machine Learning, Logistics, Robust Control, Motion Planning, Sensor Fusion
Timeframe
10/2019 - 9/2021
Project Management FHOÖ
- FH-Prof. DI (FH) Dr. techn. Roman Froschauer
- DI (FH) Raimund Edlinger, MSc
Website
https://projekte.ffg.at/
Funding
The HOPPER (FFG #873987) project is funded by the Austrian Research Promotion Agency FFG in "ICT of the Future".
Partners
AIT Austrian Institute of Technology GmbH (Overall-Coordination)
Industrie-Logistik-Linz GmbH
SCHENKER & CO AG
University of Applied Sciences Upper Austria Research & Development
Palfinger Europe GmbH